Everything about Architectural
Model-Making
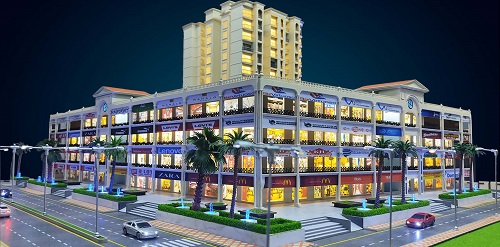
The concept of ‘Architectural Model making’ has been there since time immemorial. But the use of architectural models has evolved over the years. Earlier it was just used as a piece of decoration or as a gift. But with modernization things evolved and architectural models came to be used for proper visualization of project ideas before the final project came to life. Through this article/blog we will try to gather an understanding of architectural model making.
Architectural Model Making – An Overview
The architectural model of a project is comparable to a 3-dimensional representation of the concept that was first sketched out on paper.
The architectural model is used to share the scope of a project or to understand the spatial interrelationships. The model gives life to the project even before it stands tall in front of you.
The architectural model enables the developers (architects, designers, etc.) to understand and test how the final output of the building will look like, how the various elements of the project will interact with each other including the natural elements like wind, sunlight, landscaping etc. This is all done in a scaled-down version of the original.
For a common person, it is difficult to understand the idea that an architect or an (interior) designer has visualized. So, the architectural model is created in a very engaging and visually attractive manner. A model ultimately tells a story at a glance. It bridges the gap between an idea and reality.
Purpose of Architectural Models
Architectural models, also known as scale models, are created to serve a variety of purposes. These steps can be used to divide the procedure of developing an architectural model:
Before construction stage:
1. Aligns the design and final output
Before the construction starts, architects use the scale model to explain and align with different stakeholders like builders and (interior) designers.
The architectural models also play a very vital role in bringing to the forefront the structural inconsistency in the design (if any) or helps in understanding a construction challenge that may occur at a later stage. A timely understanding and a solution of these issues during the design stage itself help save cost and effort and moreover, saves from any potential accidents.
2. Facilitates quick approvals and permissions
The model helps in showcasing the 360 degrees of the project. The company that is developing the project is able to explain all the elements, their placement, their effect on the surroundings to the authorities, and answer all their powerful queries. This fastens the approval process as everything is available for the concerned officer to see it.
3. Helps attract investments
We have all heard the saying ‘Seeing is Believing’. So, when a company approaches a bank or an investor for raising funds, having something tangible in the form of an architectural model enhances the interest of the prospective investors. It increases their confidence in the project, and they feel convinced. Thus, architectural models are a useful tool for attracting investors to your project.
4. Facilitates sales pitches
Scale models help in creating a better sales pitch. A skilled architectural model maker creates a creative and amazing visualization for clients. The scaled replica of the project is used to give information about the project, generate curiosity and sell the project. The model highlights the best features and attracts the interest of prospective buyers.
After construction stage
1. Used as a piece of decoration
Even after the project completion, the model is kept as a lasting landmark for understanding the structure at a glance by the visitors.
2. Guidance map
This is an interesting use of the architectural model. It gives you a bird’s eye view of the entire area. The model then acts as a map for you. It clearly depicts your location and guides you as to how you can reach other parts of the area. It also helps you by showing the other things that are available in the area that you can see/visit. Such models are generally used in malls, amusement parks, or big complexes.
Types of Architectural Models
1. Conceptual Design Models
It is also called an indicative model. Made in the initial stages of the project, this model type is built to understand the basic structure or to understand a particular element in-depth of the project. This model is made at low cost using less expensive material. Most of the time these models may not be closer to the actual product also and might need many modifications. It only illustrates the idea..
2. Working Models
The working models are made post the conceptual design stage when the design is a little finalized and all elements fall into place. It will involve minute details displaying each specification with working elements. It may showcase the actual working of the project like a removable roof to get a closer look at the interiors, vehicle movement, steam flowing out of the chimney, product movement from one place to another within the model premise, machinery operating, etc. It is a good option to use in sales pitches or while taking approvals.
3. Presentation Models
These models are used for presentation purposes in exhibitions, trade fairs, or as display pieces in offices or sites. They have a higher level of detailing in them as compared to the conceptual design model. This model is made with sturdier and better material, as it needs to be more appealing to the eyes and at the same time needs to be durable.
There is one aspect that is very important while building the models under all the three categories and that is ‘Lighting’.
A model should be well-lit to stand out. There are various ways to add light to the models.
- The entire model can be illuminated at one go or,
- Lights in some parts are continuously kept on and, in another part, it lights up at regular intervals to highlight that section or a feature or,
- A combination of light is switched on intermittently to create a light play.
The model lighting can be controlled in many ways through:
4. Control panels
A touch screen panel is fixed near the model. The users can interact with the model using this panel. They can control the lighting, they can start, stop the functioning of an element by giving a command via the control panel (in case of a working model). It is a widely used concept today.
5. Control stations
This is a more traditional, less expensive, and user-friendly approach for lighting. This station has multiple buttons placed on it helps the controller/user to control the lights in the entire model. The lights on the station for a particular section can be grouped and placed together for easy understanding and a smoother control.
6. Devices
With the technological advancement nowadays mobile apps, laptops, iPads, etc. are extensively used to control the lighting effect (that was earlier controlled through switches). With further innovation, the upcoming feature is controlling lights and other aspects in the model through hand gestures (or physical gestures). This will give better control to the users.
Scale selection of Architectural Models
This is a fascinating aspect of the development of scale models. The decision on the scale largely depends on factors like the budget, the time available, the material available, the transportation aspect, the display area, etc. Depending upon the type of the project, the model can be developed with the following scales mentioned in the table:
Materials used for building Architectural Models
Once you have decided the type and scale of the model, then the next important decision that an architectural model-making company must take is on the material that will be used. The material decision can be based on several factors:
- Technical requirements
- Aesthetics
- Should be a stable, tough, long-lasting, and durable material
- Should withstand temperature variations and environmental factors like moisture, dust, and humidity.
- Should not be too complicated to handle and difficult to maintain in the long run
- Often many different materials are used in making one single model
The right selection of the material brings forth the company’s years of experience and a stronghold on architectural model-making skills.
A variety of things are at the disposal of the creative architectural model maker to build the model. Each material has its own advantage and usage while developing a model.
1. Wood
A good, strong material to build the models. The two most used types of wood are Balsa wood and Basswood.
Balsa wood is hardwood, easy to cut, sand, and carve. It gives a clean, professional output. And Basswood is heavier than Balsa making it slightly harder to work on it. But the model made with these wood types lasts long.
2. Foam
The regularly used foam types are Styrofoam, form boards, blue foam, etc. This is a favored material for the students as it is less expensive and can help in building a model in a short time.
3. Acrylic
It is a light and flexible material. It can be used to produce a lot of elements of the model like doors and windows. But one should be adept at using laser machines to cut acrylic in desired shapes and sizes.
4. Cardboard
A very common and widely used material. It is both less expensive and can be recycled thus saving cost. Models made with this material are easy to handle.
5. Metal
This material augments the appearance. Various types of metal sheets like aluminium plates, copper sheets, and many other types are used to build a model. To give it a good finish the metal is properly polished.
6. Glass
A less-used material. Majorly used to enhance the aesthetics of the model.
7. Other Material
Various other materials like metal rods, PVC pipes, etc. are used to create the landscaping, roads, streetlights, topography, and other aesthetic elements.
Maadhu Creatives have Skilled, professional and creative and architectural model makers in India and around the world are becoming more aware of their responsibilities towards the environment and thus opting for the use of eco-friendly materials like eco-friendly ink formulations, colors, etc.
Architectural model making process
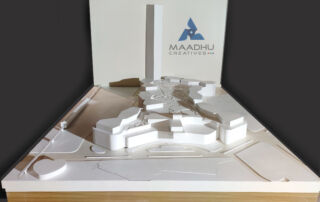
Now that all-important decisions on the purpose, the material to be used, etc are finalized then comes the operational stage (i.e.) the stage where the actual work on building the model begins.
1. Finalized design
In this stage, a professional architectural model maker first and foremost will ensure that the entire requirement is clearly gathered from the client with a finalized drawing. Having clarity on the requirement is the key to customer satisfaction. A good model is a model that is good to see and conveys the exact idea that has been visualized.
2. Laser-cutting design
Based on the finalized project design, another design is prepared for laser cutting purposes. Elevation cutting of the structure and various pieces of the model (like windows, doors, etc.) are laser cut to precision to give it a smooth and professional look.
3. Assembling the model:
When all the pieces are designed and made to match the requirement then the assembling of all the parts starts.
Post structure assembling is completed; the next step is the beautification of the model. The assembled structure is painted, required landscaping is added, and proper light fittings are done. Proper lighting in the model is very important to give a complete view of each section and element in the model.
5. 3D printing of elements
With technological developments in this field, the architectural model makers in India are opting for 3-D printing. A lot of detailing elements like human figures, doors decorative pieces, etc. are 3D printed for scale model making.
6. Finishing touches
4. Painting, Landscaping, and Lighting the model
before delivery final touches are given to the model to ensure everything is properly placed, painted and all lights are in working condition.
7. Delivery of the model
Once all is done and checked, (re-checked) the delivery of the model is done to the designated place with all safety measures to protect it from any damage.
The process may end with the delivery of the product, but the model needs a lot of care and maintenance for it to last long and serve the purpose.
Maintenance of Architectural Models
A lot of effort goes into scale model-making. The client must ensure that the final product is transported safely, stored securely, and maintained regularly.
1. Safe transportation
Always use experienced transport company with well-trained staff while shifting the model from one place to another. Pack the model in robust and shock-resistant packages to prevent damage.
2. Store securely
While storing the model in the offices or at sites chose a location where there is minimal sunlight to prevent color fading and degradation due to heat. A proper temperature should be maintained.
Install glass or acrylic cover for the model, if required. This will prevent it from damages that may happen due to visitors (especially kids) trying to touch the model.
And some spare parts of some of the essential elements of the should be kept readily available. A damaged model will lose its appeal.
3. Regular Maintenance
A periodic check should be performed to prevent it from water or insect damage. A timely inspection will help prevent large-scale damage. Dry clean the models, their covers, and their different parts properly from time to time by using a special type of vacuum cleaner and a soft cloth.
Considering the huge cost involved in getting a new model developed, it is a sensible decision to spend some money on proper maintenance of the same model to make it last longer.
Maadhu Creatives is a world class, professional architectural model maker in Mumbai. We are one of the most trusted scale model makers in India providing affordable services. Our aim is to achieve customer satisfaction and loyalty through best-in-class model making services. We also strongly believe in keeping up with the latest technology and innovation and try to incorporate it in our architectural model making services.